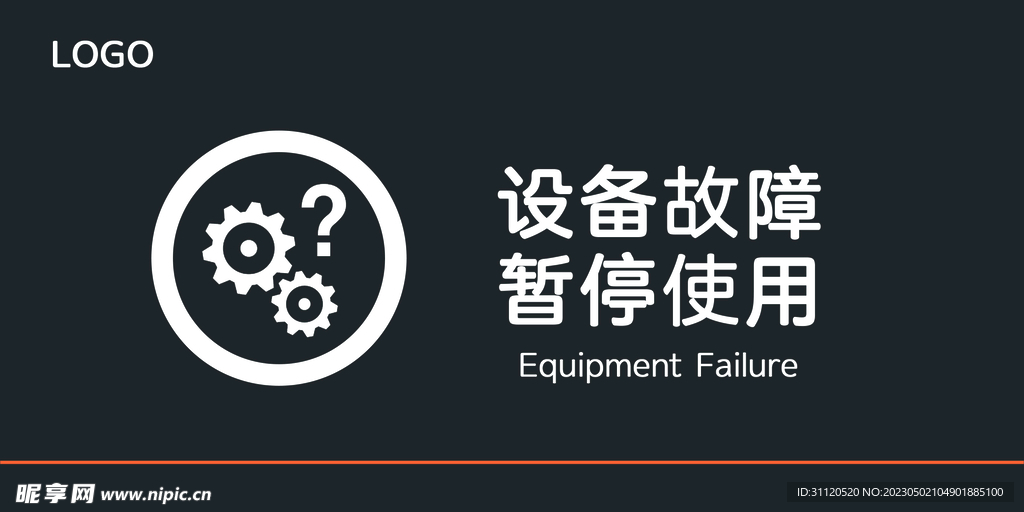
一、引言
在现代工业生产过程中,设备故障是不可避免的现象。
设备故障不仅会影响生产效率和产品质量,还可能对企业造成经济损失和声誉损害。
因此,对设备故障原因进行深入分析,并采取相应的整改措施,对于保障企业正常运营至关重要。
二、设备故障原因概述
设备故障的原因多种多样,可归结为以下几个主要方面:
1. 设计缺陷:设备在设计阶段未考虑到实际使用中的某些因素,如负荷、材料、环境等,导致设备在使用过程中容易出现故障。
2. 制造质量:设备制造过程中的质量问题,如零件精度不足、材料强度不够等,都会影响到设备的性能和使用寿命。
3. 安装调试:设备在安装、调试过程中的不当操作,如参数设置错误、设备位置选择不当等,可能导致设备在使用过程中出现故障。
4. 维护保养:设备使用过程中缺乏必要的维护保养,如润滑不足、清洁不到位等,会导致设备磨损加剧,性能下降。
5. 操作失误:操作人员技能不足或操作不当,如违规操作、误用设备等,也是设备故障的常见原因。
三、设备故障原因深入分析
为了更准确地找出设备故障的原因,我们需要对具体案例进行深入分析:
1. 案例一:某化工厂的生产设备在运行过程中突然出现性能下降。经过分析,发现是由于设备的关键部件材质不耐腐蚀,导致在特定环境下性能下降。
2. 案例二:某企业的生产线在高峰期间频繁出现故障。调查发现,部分设备的传动部件制造精度不足,导致设备运行不稳定。
3. 案例三:某工厂的机械设备在安装后调试困难。原因是设备安装时位置选择不当,导致设备运行过程中的负荷分布不均。
通过对这些案例的分析,我们可以发现设备故障的原因不仅涉及设计、制造、安装等环节,还与使用环境、维护保养以及操作水平密切相关。
四、整改措施
针对以上分析的设备故障原因,我们提出以下整改措施:
1. 设计优化:针对设备设计缺陷,与设计单位合作,对设备的关键部件进行重新设计,提高其适应性和耐用性。
2. 制造质量提升:加强供应商管理,提高设备制造过程中的质量控制,确保关键部件的制造精度和材质强度。
3. 安装调试规范:制定严格的设备安装和调试规范,确保设备安装位置正确、参数设置合理。
4. 维护保养制度:建立完善的设备维护保养制度,定期对设备进行维护保养,确保设备处于良好的运行状态。
5. 操作培训:加强操作人员的技能培训,提高操作人员的素质,确保操作人员能够熟练掌握设备的操作和维护技能。
6. 建立监测预警系统:通过引入先进的监测设备和技术,建立设备故障预警系统,及时发现和解决潜在问题。
7. 持续改进:定期对设备进行性能评估和使用反馈收集,针对发现的问题进行持续改进,不断提高设备的性能和可靠性。
五、实施效果与监控
为了确保整改措施的有效性,我们需要实施以下监控和评估机制:
1. 实施跟踪:对整改措施的落实情况进行跟踪和记录,确保整改措施得到贯彻执行。
2. 效果评估:定期对整改效果进行评估,分析整改措施对设备性能和使用寿命的影响。
3. 持续改进:根据评估结果,对整改措施进行持续改进和优化,提高设备的运行效率和可靠性。
六、结论
设备故障是企业面临的重大问题之一。
通过对设备故障原因进行深入分析和采取相应的整改措施,我们可以提高设备的性能和可靠性,保障企业的正常运营。
整改措施的实施需要企业各部门的协同合作和持续努力。
因此,建立长效的监控和评估机制至关重要。
只有这样,我们才能在面对设备故障时迅速响应并解决问题同时确保企业的生产效率和产品质量不受影响。
电气故障产生的主要原因是: 1、发电机发出的电压偏低、频率偏低 解决办法:测量熔断器管座两端,如果阻值小于0.5欧姆,就认为正常;如果阻值为数欧,则认为接触不良,需要进行处理;如果阻值超过10千欧,则认为断线不通。 2、电气设备结构损坏、绝缘材料的绝缘击穿 解决办法:电流表串接到电路中,然后在不同的地方进行短接 。 3、电路存在接触不良。 解决办法:在比较黑暗和安静的情况下,观察电路有无火花产生,聆听是否有放电时的“嘶嘶”声或“劈啪”声。 如果有火花产生,则可以肯定,产生火花的地方存在接触不良或放电击穿的故障 总结电气故障产生的原因按照上面的步骤进行排查,很快就能解决问题。